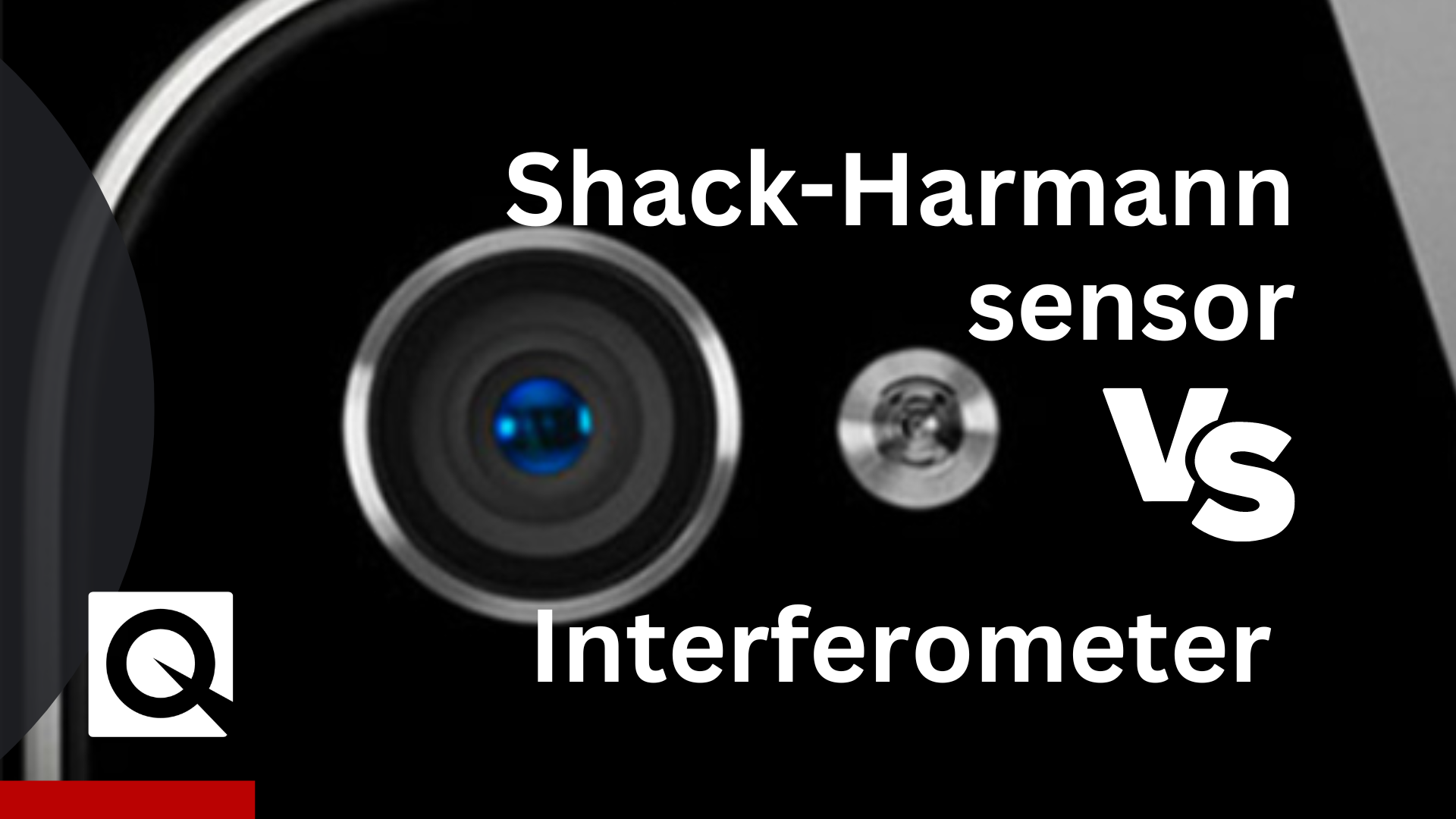
A Shack-Hartmann wavefront sensor is an optical system that can detect wavefront errors. Like an interferometer, these sensors can be used to measure the shape and transmission quality of optics. While inexpensive, Shack Hartmann sensors have significant drawbacks that limit their effectiveness to a somewhat narrow band of applications.
What is a Shack-Hartmann Wavefront Sensor?
The Shack-Hartmann sensor consists of a detector with an array of lenslets in front of it. Each lenslet focuses a portion of the pupil to a spot on the detector.
When the incoming wavefront is planar, the spots on the detector will appear in a regularly spaced array. Any deformation in the wavefront will cause the spots to move on the array. By analyzing how much each spot has moved one can determine the error in the incoming wavefront.
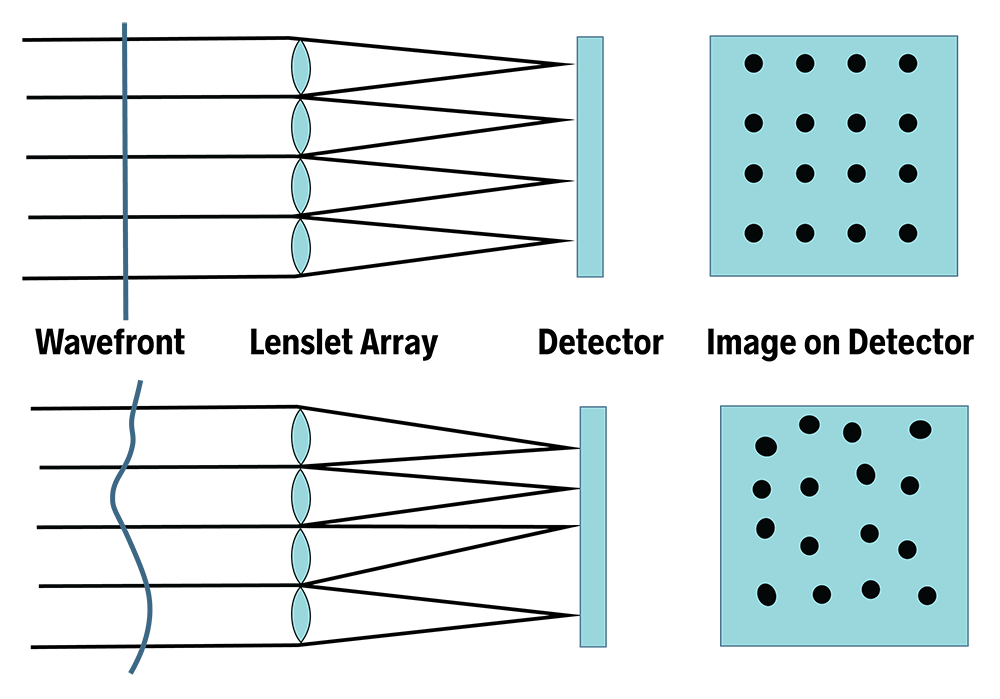
Application: measure low-order errors quickly
A Shack-Hartmann sensor provides a simple, inexpensive method for measuring lower-order errors in transmitted wavefronts. The sensor is also well suited for measuring optics with high slopes and wavefronts with large deformations. It can , with some adaptation, be used to measure surface shape.
Low- to mid-quality small optics, such as those in cell phone cameras, can be measured quickly in automated test stations. Because only a single measurement is required, acquisition time can be very fast, which makes a Shack-Hartmann sensor a good choice for guiding adaptive optics.
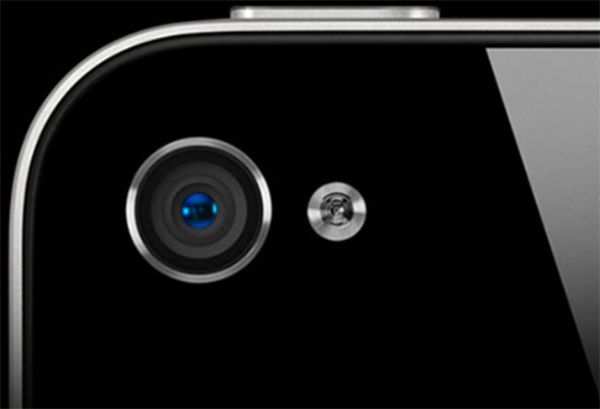
Where a Shack-Harmann sensor cannot perform
The Achilles heel of a Shack-Hartmann sensor is its limited sampling. The lenslet array typically includes 75×75 spots or less, meaning measurements must be based upon roughly a few thousands spots (compared to millions of pixels in a typical interferometer sensor). Because of this limited sampling, a Shack-Hartmann sensor cannot accurately measure higher order shape errors.
Measurements of larger optics are also suspect, since dispersing such a small array of spots over the surface requires large distances between data points.
Accuracy is another important consideration. Much of the math involved in converting the spot pattern to shape error is based on the linear translation of each spot. However, in a real-world system the spots elongate as well as translating, which can lead to accuracy errors.
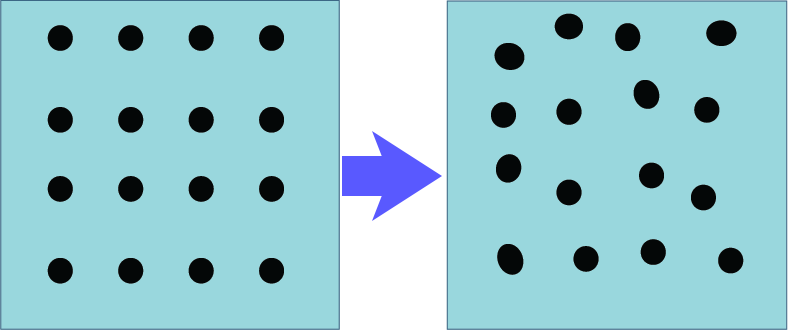
It is no surprise, then, that most Shack-Hartmann manufacturers use an interferometer as the standard against which to compare the accuracy of their sensors.
A laser interferometer provides better resolution and expanded functionality
A laser interferometer provides far more flexibility over a much wider range of measurements. The far superior resolution of the interferometer enables greater accuracy for measuring flat and focal optics, from a few millimeters to many meters in diameter. Advances in interferometry, such as 4D Technology’s Dynamic Interferometry®, have enabled extremely fast acquisition speeds which by and large negate the speed advantage of the Shack-Hartmann sensor as well.
For a limited set of applications, the Shack-Hartmann sensor can be a fast, low-cost method for verifying optics. But for measuring most conventional and high-quality optics, an interferometer is a far superior option due to its much higher flexibility, accuracy and resolution.
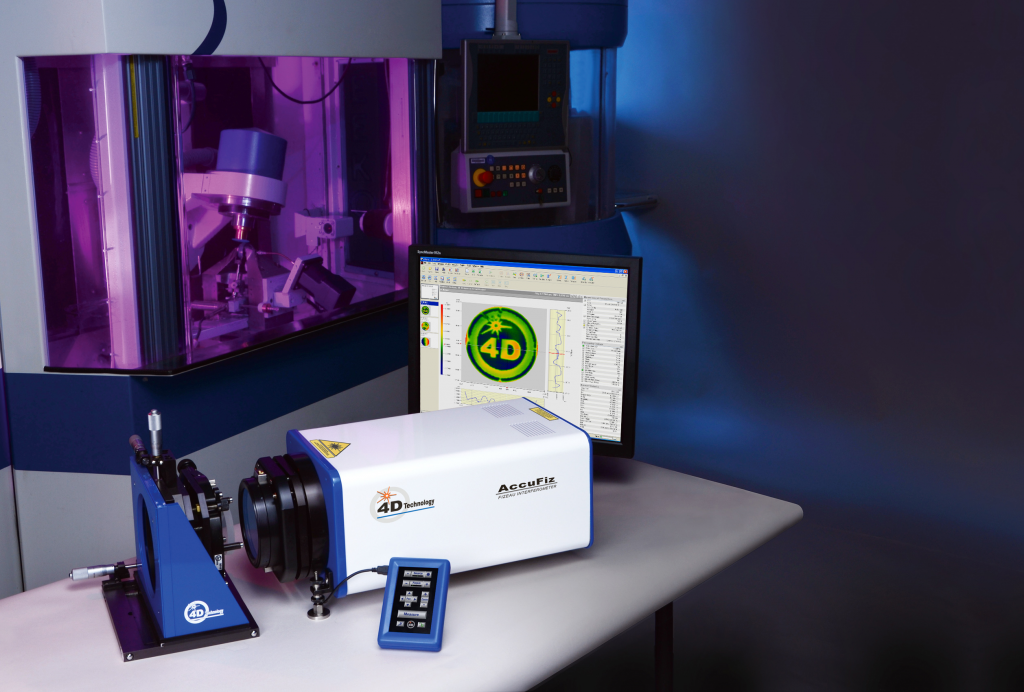
Interferometer Products
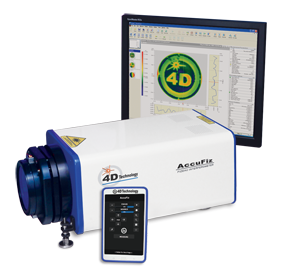
AccuFiz Fizeau Laser Interferometers
Flexible, proven and affordable, AccuFiz Fizeau laser interferometers fit well in confined lab spaces and offer high stability in any environment. In wavelengths from 355 nm through 1.064 µm and apertures from 33 mm to 600 mm, AccuFiz systems are available for a vast range of applications.
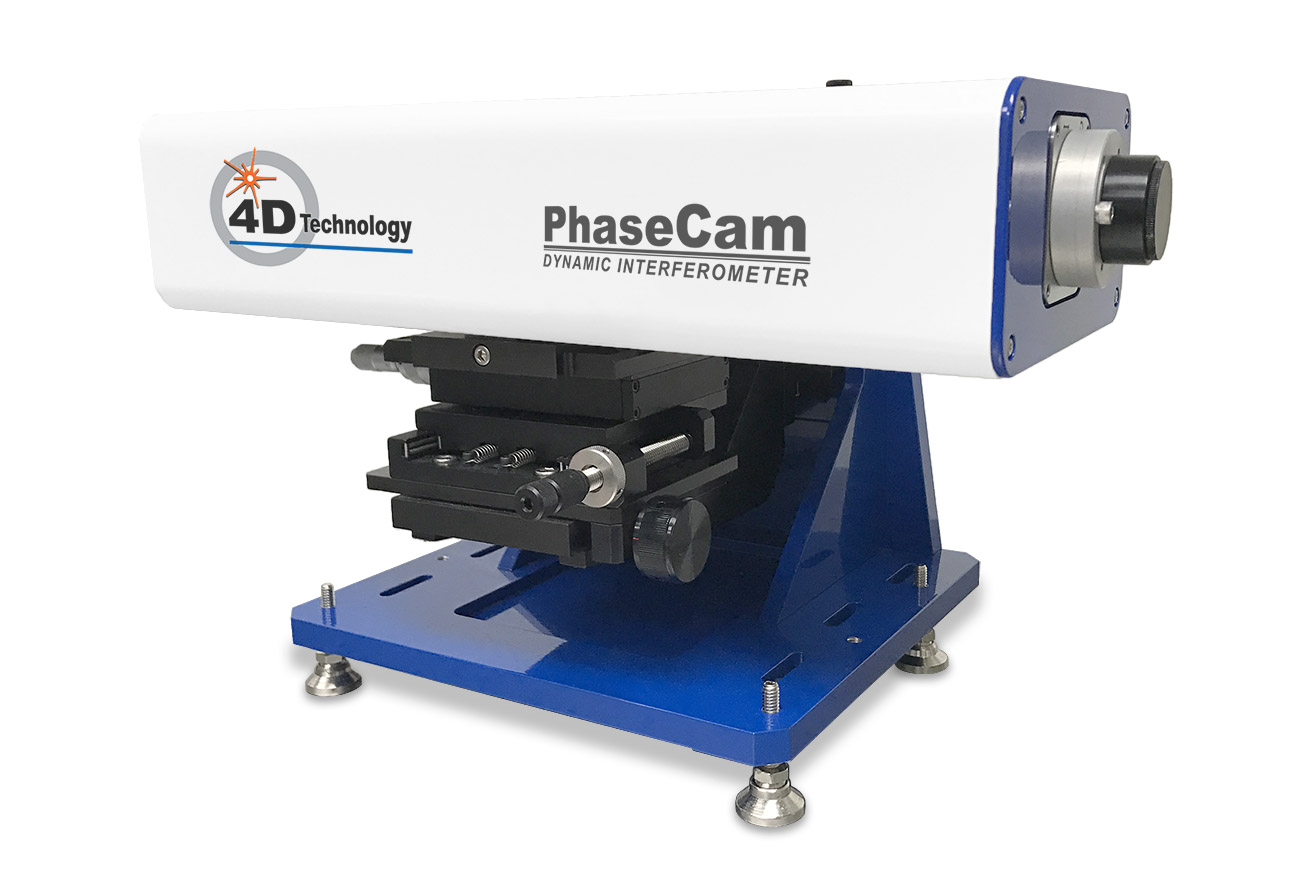
PhaseCam Twyman-Green Laser Interferometers
High resolution measurements despite vibration and air turbulence. Fast, compact and lightweight for measurement in challenging applications and environments.
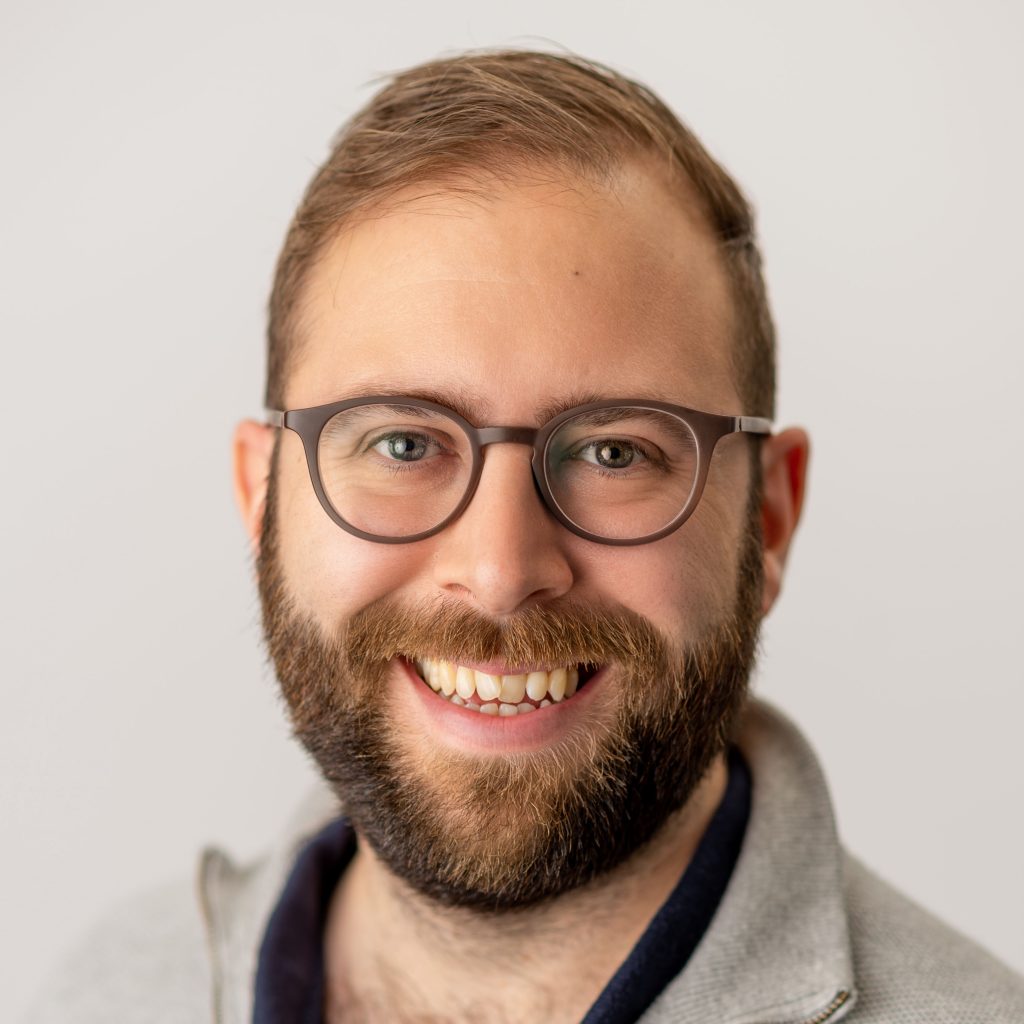
Do you have any questions?
To discuss your application and how interferometry can help, please call our Technical Sales Manager, Dr. Luke Nicholls by email or call (01372) 378822.