
App note uses the Montana Instruments Cryostation®
BACKGROUND Noise figure (NF) is a measure of how much noise a device adds to a signal relative to an ideal, noiseless device. It quantifies the degradation in the signal-to-noise ratio (SNR) as a signal passes through a system and is measured. A lower noise figure means the device adds less noise to the signal and a higher noise figure means the device adds more noise. Noise figure is defined as the ratio of the input SNR to the output SNR:
Expressed in decibels (dB):
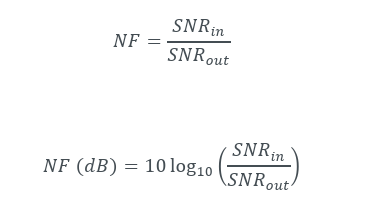
Noise parameters are a set of values describing the noise performance of a device, typically for different operators such as frequency, input impedance, and temperature. The four most often used noise parameters are:
- Fmin: The minimum noise figure a device can achieve under optimal operating conditions.
- Rn: Equivalent noise resistance, which describes how the noise figure degrades as input impedance changes from the optimal source impedance.
- |Γopt|: Magnitude of the reflection coefficient of the optimal source impedance for minimum noise.
- Γopt<: Phase of the reflection coefficient of the optimal source impedance for minimum noise.
These parameters describe how the noise figure of a device changes with varying source impedance. An impedance tuner is an important piece in a noise parameter setup, allowing users to vary the source impedance presented to a device under test and measure the resulting noise power, from which the noise parameters can then be extracted.
The most common impedance tuners are electro-mechanical in design. However, these tuners are not suitable for cryogenic environments due to their large size, mechanical operation, and the amount of heat generated by the tuners. Solid-state impedance tuners, on the other hand, provide a working alternative for cryogenic impedance tuning. The CTseries cryogenic automated tuners from Maury Microwave are rated to operate below 4K temperatures to present electronically varied impedance states to a device under test (DUT). Weighing under 80 grams with a footprint of 60mm x 40mm, as well as consuming less than 0.2 mW, the CT-series cryogenic impedance tuners are ideal for operation in a cryogenic environment. An integrated temperature sensor ensures that the temperature inside the tuner is known. An integrated bias tee allows for the optional biasing of the DUT source, while external biasing can be used to bias the load of the DUT. Coupled with a thermally stable (<20 mK, peak-to-peak), easy to use Montana Instruments Cryostation®, users can conduct noise parameter measurements in an optimal cryogenic environment that cools to below 4 K with the push of a button. Montana Instruments systems are configurable with DC, RF, or fiber feedthroughs to allow access to the cold sample space. Figure 1 shows a detailed setup of the system, with the Montana Instruments cryostat and user touchscreen on the left.
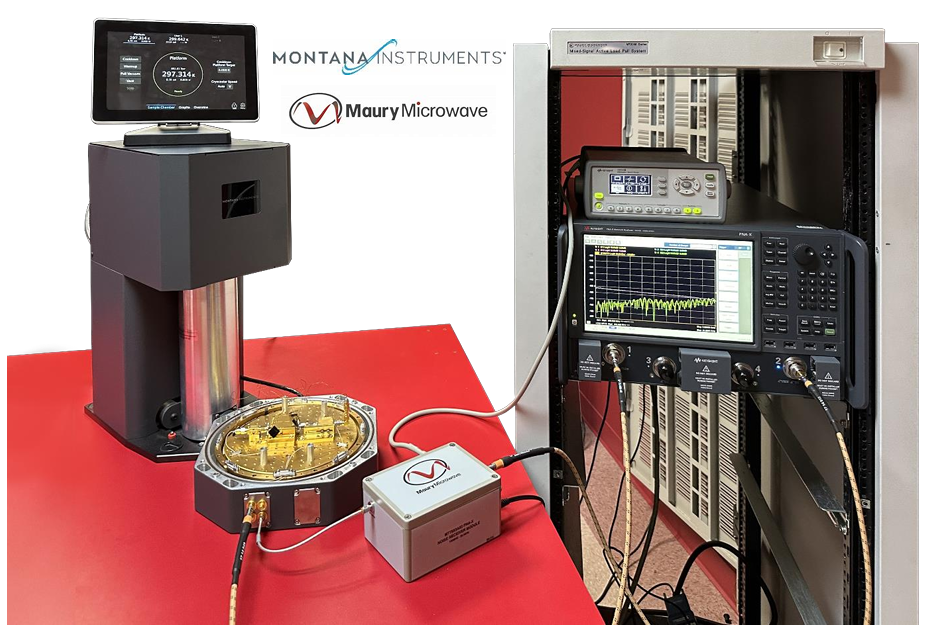
How is 4 K Reached?
Montana Instruments systems use a combination of components to reach temperatures of below 4K: a cryocooler, a helium compressor, a vacuum system, and a control system. The system can also be configured with DC, RF, or fiber vacuum feedthrough panels that terminate in the sample space. Montana Instruments cryostat system is a closed-cycle (dry) system, meaning that no liquid helium is required and the helium used is recycled through the system. Figure 2 shows the system in more detail.
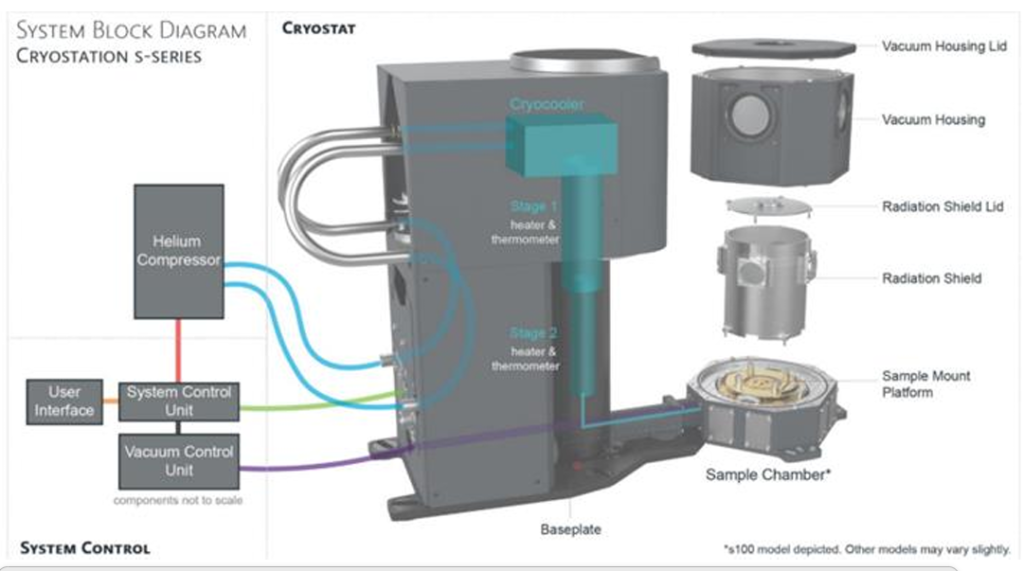
Cryocooler: Montana Instruments systems use a Gifford-McMahon (GM) cryocooler as the basis for the system.
Compressor: A helium compressor creates high- and low-pressure sections in the system to move helium gas and compress it.
Vacuum Control Unit: In order to achieve extremely cold temperatures, a vacuum must first be created in the vacuum space to remove molecules that will otherwise freeze onto the sample.
System Control Unit and User Interface Touchscreen: In house developed software allows for communication between all of these components. Temperature control allows for precise measurement and control of system temperature from room to base temperature. By automating much of the system, users are able to cool the system down with the push of a button on the user touchscreen (or remotely via ethernet connection). Changing DUT can be done in a matter of minutes once the system is warm and vented. The breadboard allow easy integration of imperial and metric form factors. The available sample space and electrical connection capabilities allow cooldown of multiple samples at once to enhance DUT throughput.
Vacuum Feedthroughs and Cryogenic Wiring: Montana Instruments cryostats can be configured with a combination of DC, RF, and fibre vacuum feedthroughs that terminate in the sample space. Wiring in the sample space allows for making connections at the sample. For more in-depth detail about cryogenic wiring and recommended best practices, please read our Cryogenic Wiring Guide.
- In more detail, a Montana Instruments cryostat operates, at a basic level, in the following order of operations:
- User selects cooldown target temperature and initiates a cooldown either by using the provided touchscreen or REST API.
- System begins to pull vacuum on sample chamber, which is still at room temperature.
- Once a target pressure is reached (a few mTorr), cryocooler and compressor turn on.
- System cooling begins.
- Through thermally connecting the cryocooler to the sample space, the sample space is cooled to 4K.
Vacuum pressure at base temperature is generally on the order of 10-8 Torr. As it is a closed-cycle, dry cryostat system, both vacuum and base temperature can be held for extended periods of time with no additional input from the user.
Experimental Setup
Figure 3 shows the diagram of a cryogenic noise parameter measurement system. The following list identifies the components in the system.
- Cryostat- Montana Instruments Cryostation® s200
- Vector network analyser (VNA)- Keysight Technologies N5245B PNA-X with integrated 029 noise receiver
- Noise figure analyser (NFA)- integrated in VNA
- Cryogenic impedance tuner- Maury Microwave CT-2G-18G
- Cryogenic termination- Quantum Microwave QMC-CRYOTERM-DC18NM
- Cryogenic VNA calibration kit- Maury Microwave MODEL
- Noise Source- Maury Microwave Noisecom NC346D
- Cryogenic and room-temperature cables and adapters- Varies
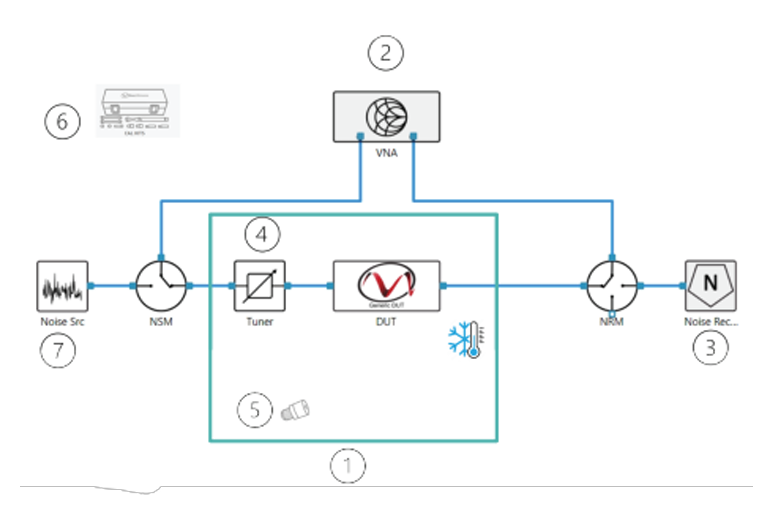
Figure 4 shows the actual system setup with the Montana Instruments Cryostation® s200 and the CT-Series Cryogenic Automated Tuner.
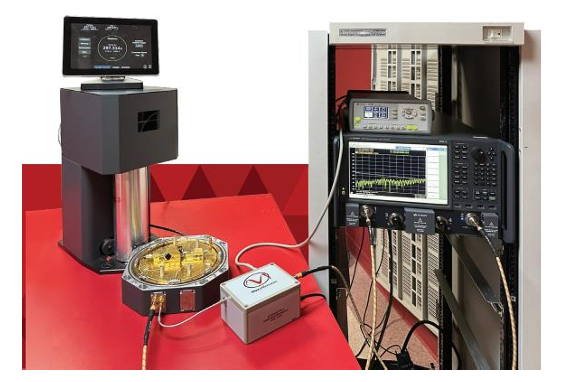
Measurement Conditions and Procedures
Noise parameter measurements were taken on a Cosmic Microwave low noise amplifier (LNA) model CITCRYO1-18, using the components listed above. In addition to the above components, a Maury Microwave noise switching module (NSM) was used to simplify the input and switch between the noise source and the VNA. A Maury Microwave noise receiver module (NRM) was used between the output of the DUT and the PNA-X to lower the receiver noise figure and improve measurement sensitivity.
The Montana Instruments Cryostation® was operated at a stable 4.2 K. This slight increase in temperature from 4 K is due to the addition of wiring in the sample space. Even in the setup shown in Figure 5, this temperature was achieved at the push of a button on the pictured user touchscreen.
Results and Discussion
Figure 5 illustrates an example of noise parameters extracted from source pull measurements.

The integration of the Cryogenic Automated Tuner with the Montana Instruments Cryostation® provides a streamlined, user-friendly and easy to use system to conduct noise parameter measurements, like the measurements taken in Figure 6.
Conclusions
Using a CT-Series cryogenic automated tuner in combination with a Montana Instruments Cryostation® provides users conducting noise parameter measurements with a thermally stable (<20 mK, peak-to-peak), easy to use sub-4K environment to work within all at the push of a button. For more information on how a Montana Instruments cryostat can benefit your experimental setup, please contact us below:

Learn more
Discuss your application with our Technical Sales Manager, Dr. Luke Nicholls by email below or call (01372) 378822.