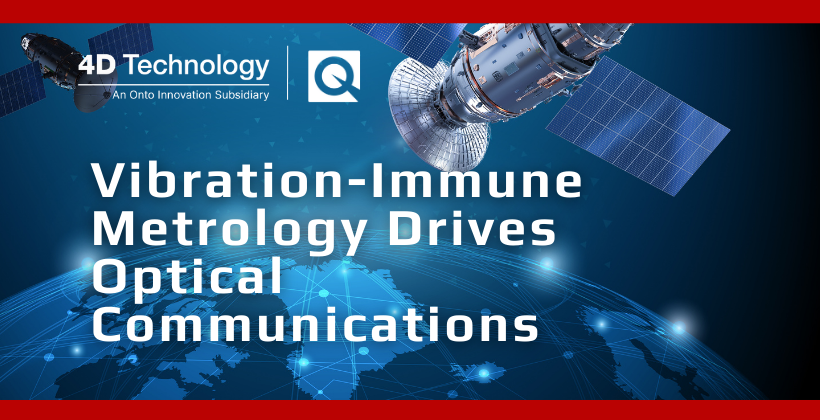
by Mike Zecchino
To keep pace with the growth of data-heavy applications, government and space agencies are investing heavily in free space laser communications. Using multiple wavelengths, laser sources can increase data transfer rates far beyond the capabilities of radio-frequency (RF) communications. But developing those data links requires optics that push the capabilities of today’s manufacturing techniques – and the metrology to verify them. 4D Technology metrology systems are leading the way, controlling wave-front error, surface figure, and surface roughness at the wavelength bands that matter the most.
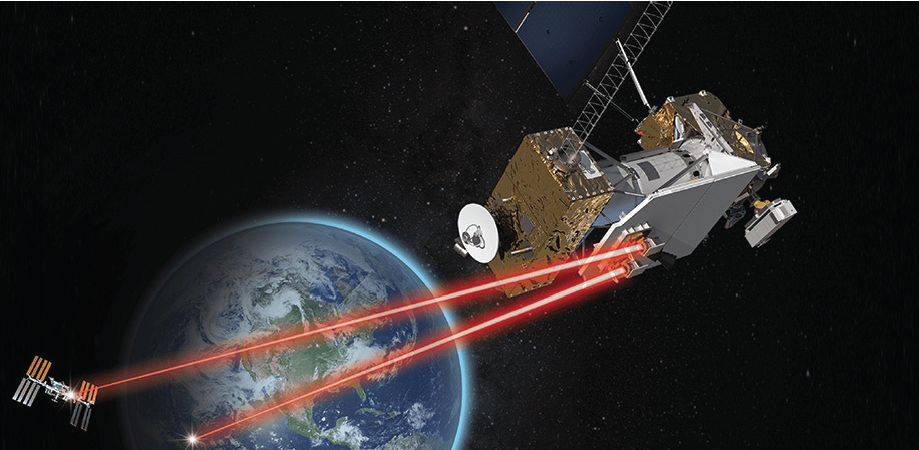
over laser links. Credit: NASA’s Goddard Space Flight Centre
What is Driving the Switch to Optical Communications?
For decades, communications companies have relied on RF communication to transmit signals. Today, however, these same companies are looking to laser-based communications for uplink, downlink, and data transfer between satellites and between earth-based stations where cable or fibre connections are not feasible. Several key factors are driving this shift.
Data Volume and Transfer Speed
Government, defense, and commercial entities are all requiring greater data volumes—and optical communications can provide thousands of times more data capability than RF systems.
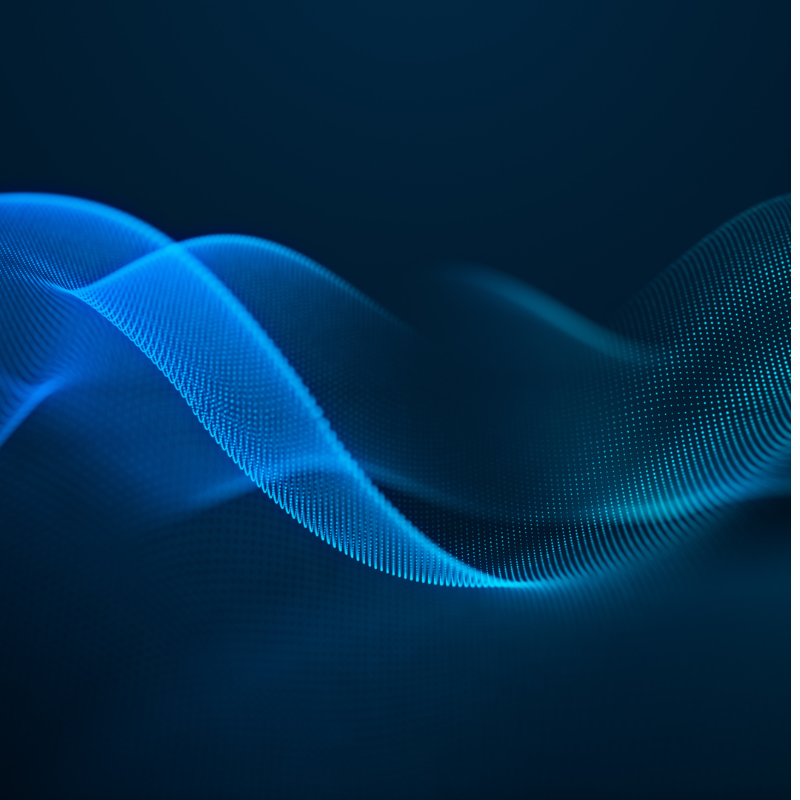
Laser-Based vs RF Communications
• Vast increase in transmission speed and bandwidth
• Smaller receivers for lighter spacecraft
• Tighter beam provides greater security
Where RF systems operate in the 300 Hz–300 GHz frequency range, optical systems can operate upwards of 300 THz. With much shorter wavelengths, an optical beam stays more focused than an RF signal as it propagates, meaning more power can be collected by the receiver, with a greater signal to noise ratio (SNR).1 By using multiple wavelength bands simultaneously, providers can dramatically increase the data rate – but the increased complexity places greater demands on the system optics.
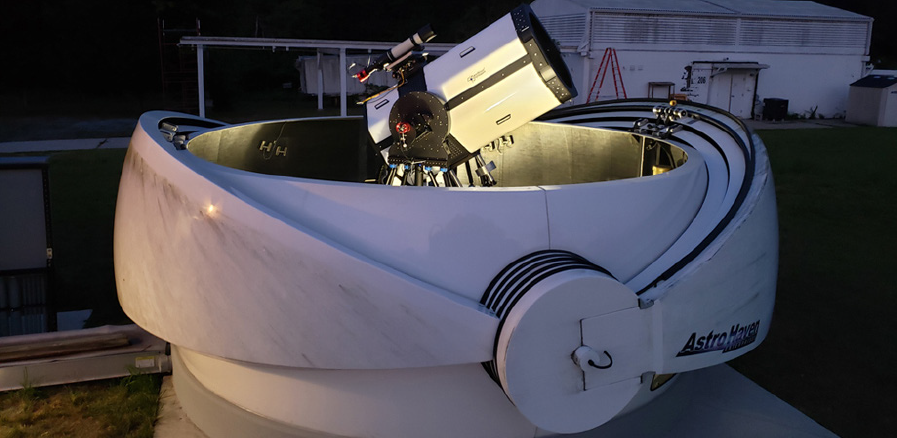
Security
Radio and microwave communications beams are wide and easily detected, making them susceptible to interception, jamming, and frequency interference. The beam returning from a spacecraft may be hundreds of kilometers wide by the time it reaches the receiver. In contrast, an optical return beam in the C band may be only tens of meters wide at the receiver. Such a tight beam improves security and makes
the signals virtually undetectable.
Cost
Optical systems can transmit massive amounts of data over longer distances using fewer and smaller transmitters and receivers. For payload satellites and spacecraft, smaller hardware translates to lighter payloads, and significant cost reductions. Because of these benefits, the earliest adopters of optical communications have been government and defense groups, along with numerous space agencies. Now
that these groups have proven the technology, and because the cost of access to space has fallen dramatically in the last decade, commercial applications are also expanding, particularly in air-to-air, maritime, and remote applications where fibre connections are impractical.
Metrology to Meet Optical Communication Challenges
The optical components and systems involved in transmitting, relaying, and receiving these signals must be held to rigorous controls. It is essential to test the components at every functional wavelength, to understand how the beams will propagate, spread, and scatter.
Earlier optical technology operated at wavelengths in the 950 nm and 1064 nm range. The industry is currently pushing to expand communication in the C-band, which has been approved for communications and heavily tested, helping increase the rate of adoption.
4D Technology has been leading the development of metrology for space-based optics since its inception over 20 years ago. The company’s instruments have been used to test optical systems for dozens of space missions and payload satellites, developing numerous innovations to ensure the quality of these optics and to ensure that that will handle the extreme demands of space.
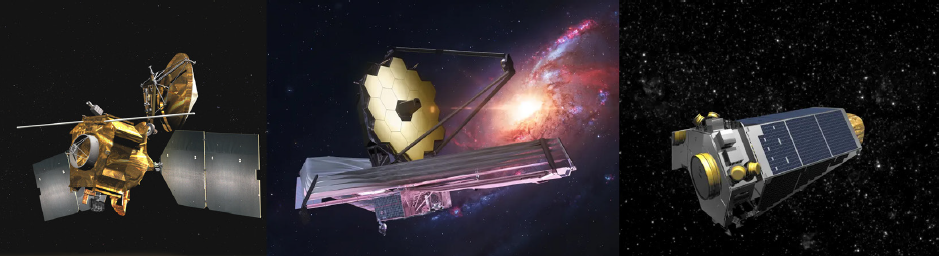
Mars imager, JWST observatory, and Kepler exoplanet observatory.
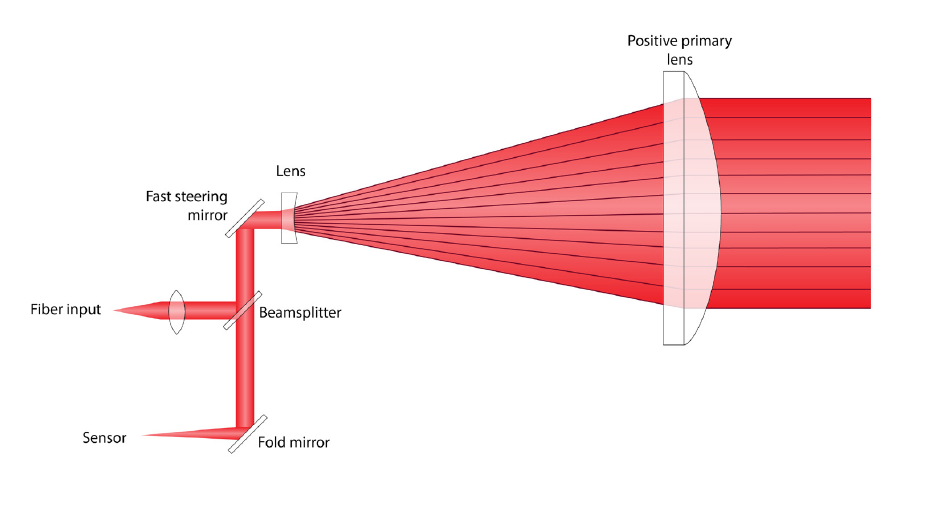
The 4D AccuFiz® SWIR Fizeau Interferometer and PhaseCam® Twyman-Green SWIR Interferometer both operate around the 1550nm wavelength. Their advantages for optical measurements include:
- compact, lightweight design that simplifies test setups
- vibration immunity enable the systems to measure in challenging environments, without isolation
- unique capability to accept external sources at wavelengths throughout the C-Band, enabling manufacturers to test optical components and systems at every operational wavelength.
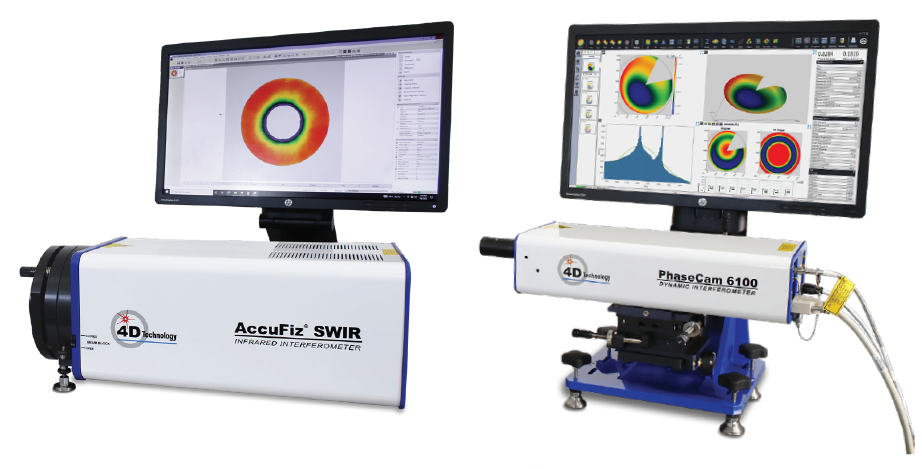
throughout the C-Band.
Measuring Despite Vibration
Dynamic interferometry enables vibration-immune, instantaneous measurement of optical components and systems. This enabling technology has proven invaluable for testing optics in:
- vibration-heavy environments, such as cryovac environmental chambers
- long cavity measurements
- small and large optics
- real time system alignment
Both the PhaseCam SWIR and AccuFiz SWIR are equipped for dynamic measurement, reducing the requirements for vibration isolation and greatly reducing the cost of testing these critical optics.
Measure at Functional Wavelengths
Both the PhaseCam and AccuFiz provide highly accurate measurement of surface figure and transmitted wavefront error, for focal and afocal optics, aspheres, optical systems and telescopes, prisms, corner cubes, etc. The large aperture of the AccuFiz is convenient for fast, repeated measurements of optical
components. The fully on-axis PhaseCam, with built-in beam ratio adjustment, excels at measuring low return systems, and measuring aspheric optics using a Computer Generated Hologram (CGH).
Real Time Alignment and Collimation
The Zernike coefficients of an optical component or system can be calculated and viewed in Continuous Mode, providing real-time feedback for quickly aligning and collimating elements of free-space optical systems.
Measuring Roughness
Surface roughness is a third, critical aspect of optics for communications. Excessive roughness can:
- scatter the beam, leading to signal loss and reduced data transfer rates
- lead to crosstalk between the various channels in multi-wavelength systems
- enhance thermal changes, leading to thermal stresses that can alter the optical shape.
The NanoCam HD optical profiler was designed specifically to measure roughness on optical grade surfaces. Robot-mounted or handheld, the NanoCam measures rapidly at multiple locations around an optic to ensure that roughness falls within all specifications.
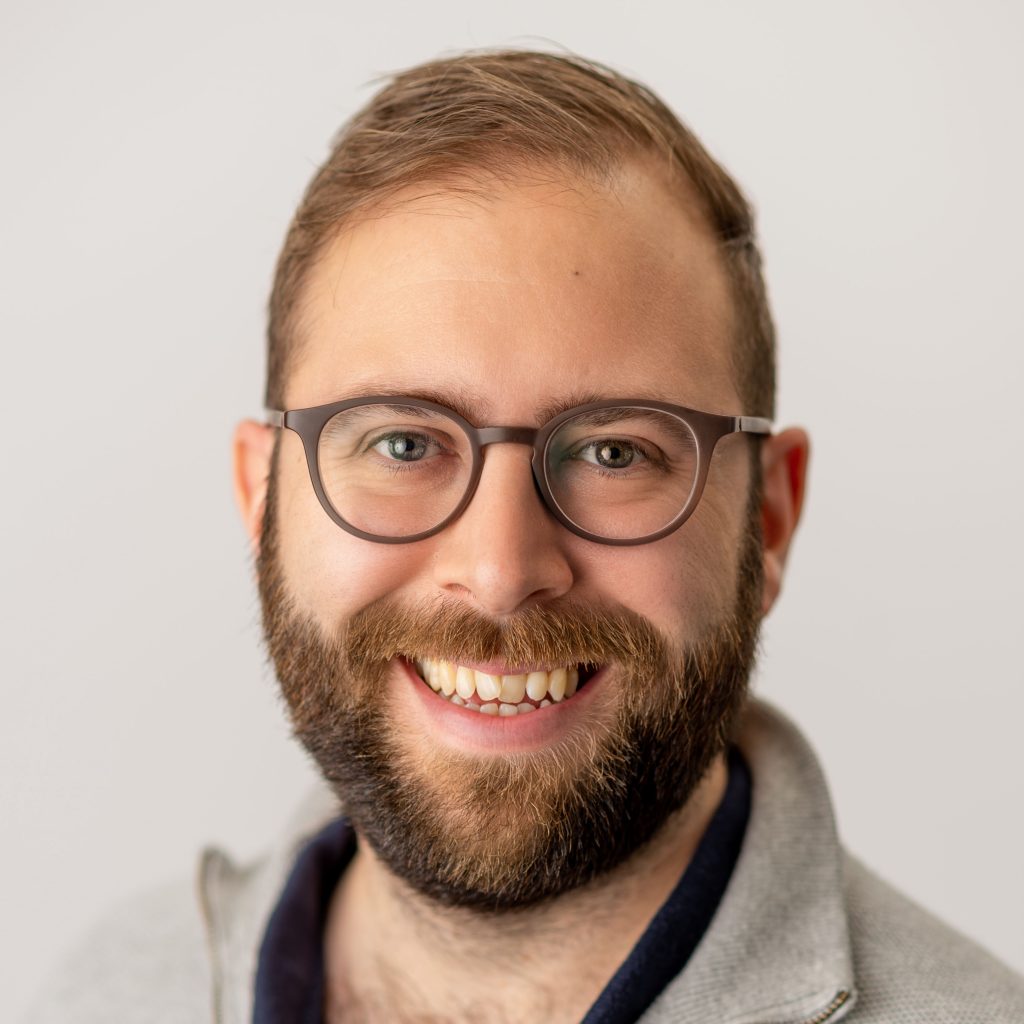
To discuss how 4D Technology interferometers can solve your satellite communications challenges, contact our Technical Sales Manager, Dr. Luke Nicholls by email or call (01372) 377882.