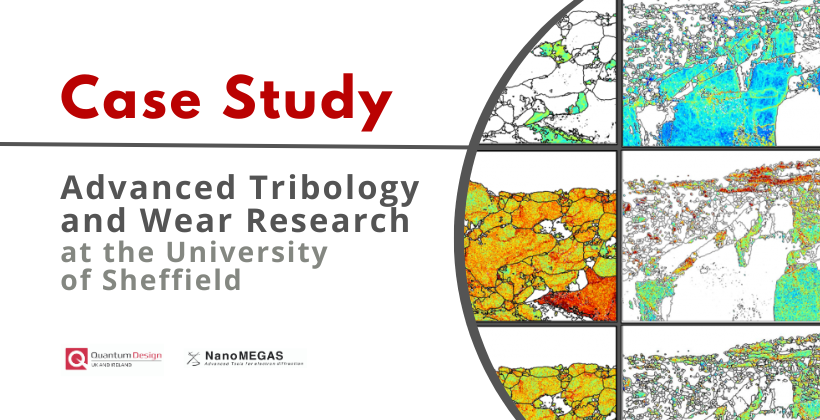
Dr Jiahui Qi
The Sorby Centre for Electron Microscopy, School of Chemical Materials and Biological Engineering, The University of Sheffield
Institution:
Tribology and Wear Lab, School of Chemical Materials and Biological Engineering, The University of Sheffield
Research Focus:
The Tribology and Wear Lab at the School of Chemical Materials and Biological Engineering, University of Sheffield, is recognised for its expertise in the high-resolution characterisation of microstructures, especially surfaces and interfaces. The lab’s research programs, led by Professor Rainforth, cover a wide array of materials science fields, focusing on developing new, high-strength materials and understanding surface phenomena that occur during wear and friction processes. The lab is integral in developing superior materials for medical implants, aerospace, and manufacturing industries.
Key Research Areas:
- High-resolution Transmission Electron Microscopy: The lab utilises this advanced technique to study atomic structures, particularly at interfaces found in nanoscale multilayer coatings and functional ceramics. This research is critical for improving the performance of materials in demanding environments.
- Tribocorrosion and Tribochemistry: A significant portion of the lab’s research is dedicated to understanding the dynamic microstructural changes that occur due to tribological contact, such as friction and wear, in both metallic and ceramic systems. The focus is on how these processes activate chemical or electrochemical reactions at the surfaces, leading to wear and corrosion in materials like hip arthroplasties and zirconia ceramics.
- Wear and Friction in Biomedical Devices: The lab extensively studies the performance of materials used in biomedical applications, such as hip implants, focusing on how frictional contact and the biological environment contribute to surface degradation. This includes studying the synergy between wear and corrosion, particularly in materials like Ti-6Al-4V and CoCrMo alloys.
- Oxidation and Surface Degeneration Phenomena: The lab also investigates oxidation during processes like hot rolling in metals and hydrothermal degradation of ceramics. Understanding these phenomena helps in designing new alloys that are more resistant to surface degradation.
- Microstructural Evolution During Metal Processing: Research is conducted on metals like titanium, magnesium, and steel to understand how their microstructures evolve during processing. The goal is to develop new materials with enhanced mechanical properties for industrial applications.
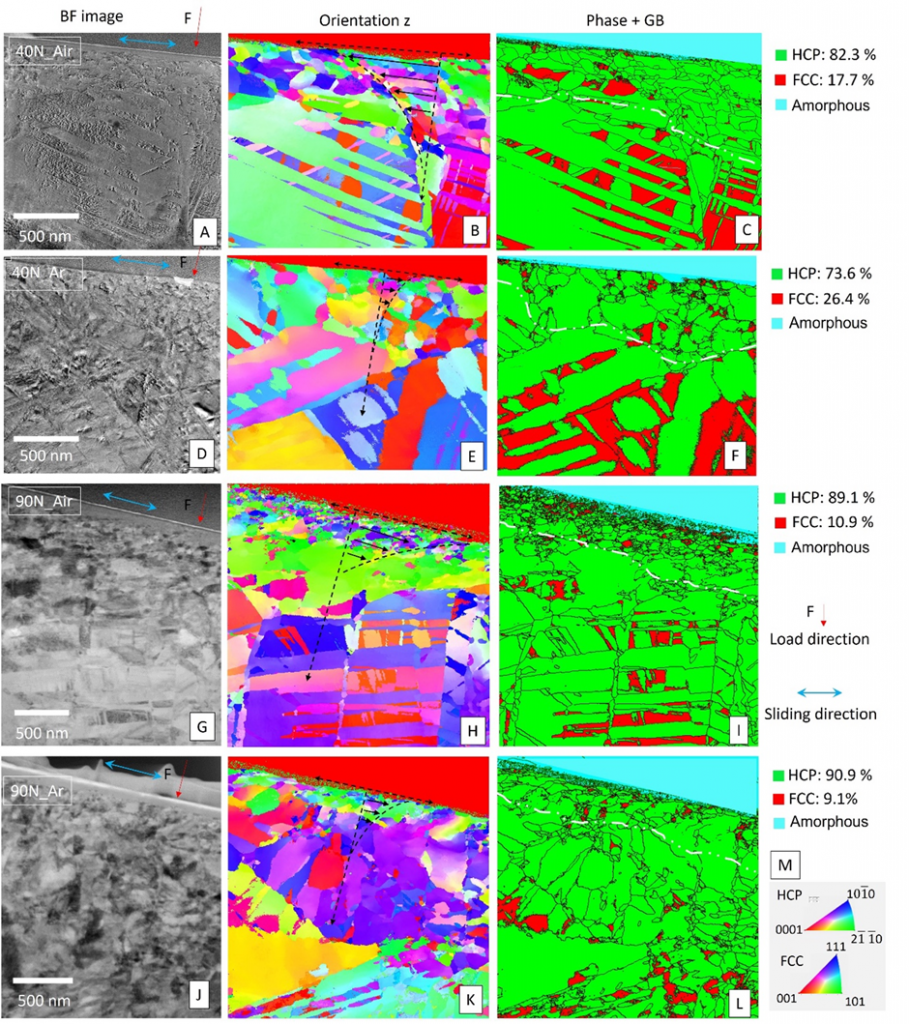
(Qi, J., et al. “Tribocorrosion behaviour of CoCrMo in simulated body fluid under anaerobic conditions.” Wear 556 (2024): 205523.)
Challenges Before NanoMEGAS:
Prior to acquiring the NanoMEGAS system, the lab encountered limitations in quantitatively interpreting the nanoscale structural changes that occurred during tribological processes. While conventional methods like transmission electron microscopy (TEM) and electron backscatter diffraction (EBSD) offered some insight, they could not fully resolve the fine details of highly deformed structures at the nano-level. Specifically, the team struggled to quantify dislocation densities and detect subtle phase transformations that influence friction and wear. This lack of precision inhibited their ability to predict and improve material performance, particularly for biomedical implants where understanding the interplay between wear, corrosion, and protein interaction is crucial.
Why NanoMEGAS?
Precession Electron Diffraction (PED): NanoMEGAS provided a breakthrough with its precession electron diffraction technology, offering spatial resolution between 0.5–5 nm and an angular resolution of approximately 0.1°. This capability allowed the lab to analyse the ultrafine, nanocrystalline structures formed under severe tribological conditions, which were previously very challenging using conventional techniques.
Resolution of Complex Structures: The ultrafine grain structures that develop in materials like Ti-6Al-4V and CoCrMo during tribocorrosion were difficult to characterise using traditional methods. PED allowed the lab to accurately index different phases and calculate dislocation densities, providing a more comprehensive understanding of the deformation mechanisms at play.
ASTAR Software Integration: NanoMEGAS’s ASTAR software enabled automated phase and orientation mapping, which was crucial for the lab to interpret the highly deformed structures efficiently. This software allowed the lab to correlate the nanoscale structural data with the wear performance of materials.
Ability to Quantify GND Density: NanoMEGAS’s capabilities to obtain data are then used for calculating the geometrically necessary dislocation (GND) density. This helped the lab evaluate the degree of deformation in different phases and under various tribological conditions. This allowed for more precise predictions regarding how materials will perform under wear and corrosion.
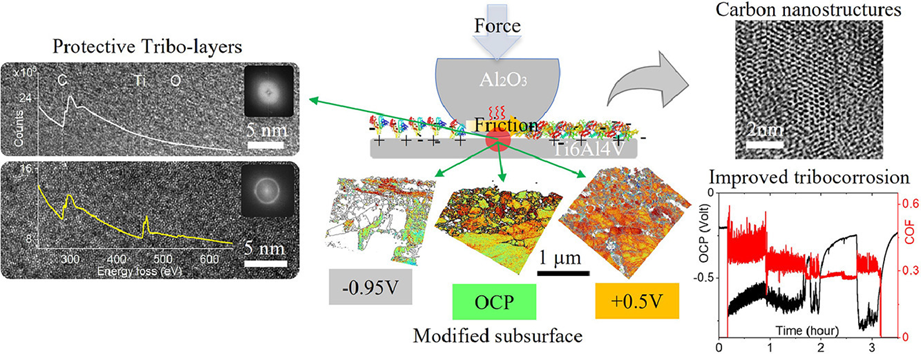
(Qi, J., et al. “Insights into tribofilm formation on Ti-6V-4Al in a bioactive environment: Correlation between surface modification and micro-mechanical properties.” Acta Biomaterialia 141 (2022): 466-480.)
How NanoMEGAS Transformed Our Research:
In one of the lab’s key research projects, NanoMEGAS played a vital role in understanding the microstructural evolution of Ti-6Al-4V and CoCrMo alloys during tribocorrosion tests conducted in a simulated body fluid environment. Tribocorrosion—an interaction between wear, friction, and electrochemical corrosion—has a significant impact on the performance of biomedical implants. Using NanoMEGAS, the lab team was able to quantitatively measure the geometrically necessary dislocation (GND) density and characterise the formation of tribofilms. The ability to measure deformation structures quantitatively at nanoscale precision was critical to uncovering how these tribofilms influence material wear resistance.
Case Study Example: Tribocorrosion of Ti-6Al-4V
The study investigated the tribocorrosion behaviour of Ti-6Al-4V, a commonly used biomedical implant material, in a simulated body fluid environment containing proteins (BSA). The research revealed that the formation of tribofilms significantly reduced friction and wear under certain electrochemical conditions, particularly at positive potentials. NanoMEGAS was used to analyse the microstructure of the worn surface, where it detected the presence of onion-like carbon structures (nanocarbon onions) within the wear debris. These findings suggested that proteins in the fluid contributed to the formation of a protective tribofilm, which improved the implant’s wear performance (Qi et al., 2022).
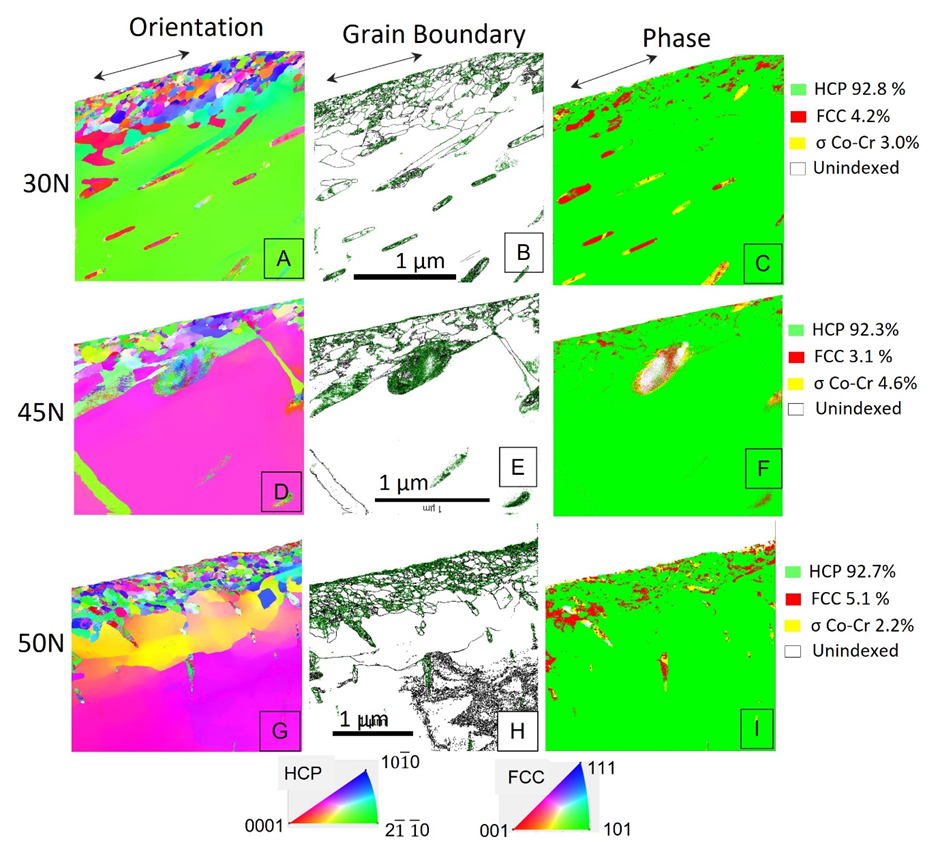
(Qi, J., et al. “Investigation of the wear transition in CoCrMo alloys after heat treatment to produce an HCP structure.” Wear 518 (2023): 204649.)
Results and Key Findings:
NanoMEGAS enabled the team to achieve several key results that were unattainable with conventional techniques:
- Quantified GND density and identified nanostructural changes under different tribocorrosion conditions.
- Detected the formation of a protective tribofilm that reduced friction and wear, particularly under conditions with a positive potential and protein interaction.
User Experience and Support:
Although the initial use of NanoMEGAS began without in-person training due to the COVID-19 pandemic, the lab was later able to reconnect with the NanoMEGAS support team for training and updates. The hands-on support significantly enhanced the team’s understanding of the system, allowing them to expand its application to more complex projects. The training helped ease the challenges of data processing and interpretation, leading to more efficient use of the system.
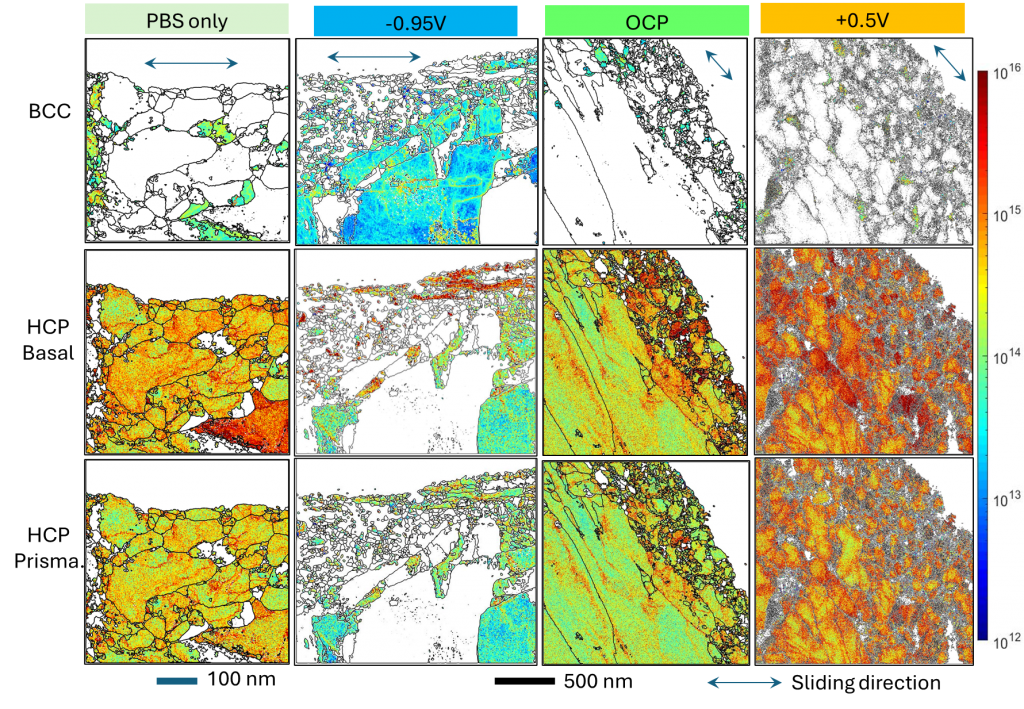
(Qi, J., et al. “Insights into tribofilm formation on Ti-6V-4Al in a bioactive environment: Correlation between surface modification and micro-mechanical properties.” Acta Biomaterialia 141 (2022): 466-480.)
Impact and Future Opportunities:
NanoMEGAS has been transformative in enabling the Tribology and Wear Lab to conduct advanced research at the University of Sheffield. The lab is now exploring new research avenues, including in situ heating experiments in TEM to observe phase transformations in real time. The data gathered using NanoMEGAS will further contribute to the lab’s ongoing research into wear-resistant materials and their application in biomedical and industrial sectors.
The lab is also enthusiastic about collaborating with other institutions and industrial partners through the Henry Royce Institute at Sheffield, offering access to NanoMEGAS through the university’s Equipment Access Scheme (https://www.sheffield.ac.uk/royce-institute/equipment-access-scheme). The team is keen to host future workshops to share knowledge and promote the system’s capabilities to the broader research community.
Conclusion:
NanoMEGAS has proven to be an indispensable tool in advancing our understanding of tribological processes at the nanoscale. Its ability to precisely characterise microstructural changes has provided invaluable insights into material performance in a wide range of applications.
For more information or collaboration inquiries, please contact the Sorby Centre for Electron Microscopy at i.ross@sheffield.ac.uk or visit The University of Sheffield Electron Microscopy Facility though this link: https://www.sheffield.ac.uk/materials/research/facilities/electron-microscopy.
List of publications:
- Qi J, Cole T, Foster A & Rainforth WM (2024) Tribocorrosion behaviour of CoCrMo in simulated body fluid under anaerobic conditions. Wear, 556-557, 205523-205523.
- Qi J, Ma L, Gong P & Rainforth WM (2023) Investigation of the wear transition in CoCrMo alloys after heat treatment to produce an HCP structure. Wear, 518-519, 204649-204649.
- Qi J, Guan D, Nutter J, Wang B & Rainforth WM (2022) Insights into tribofilm formation on Ti-6V-4Al in a bioactive environment: Correlation between surface modification and micro-mechanical properties. Acta Biomaterialia, 141, 466-480.
- Xu Y, Qi J, Nutter J, Sharp J, Bai M, Ma L & Rainforth WM (2021) Correlation between the formation of tribofilm and repassivation in biomedical titanium alloys during tribocorrosion. Tribology International, 163, 107147-107147.
- Namus R, Nutter J, Qi J & Rainforth WM (2021) Sliding speed influence on the tribo-corrosion behaviour of Ti6Al4V alloy in simulated body fluid. Tribology International, 160, 107023-107023.
About Dr. Jiahui Qi
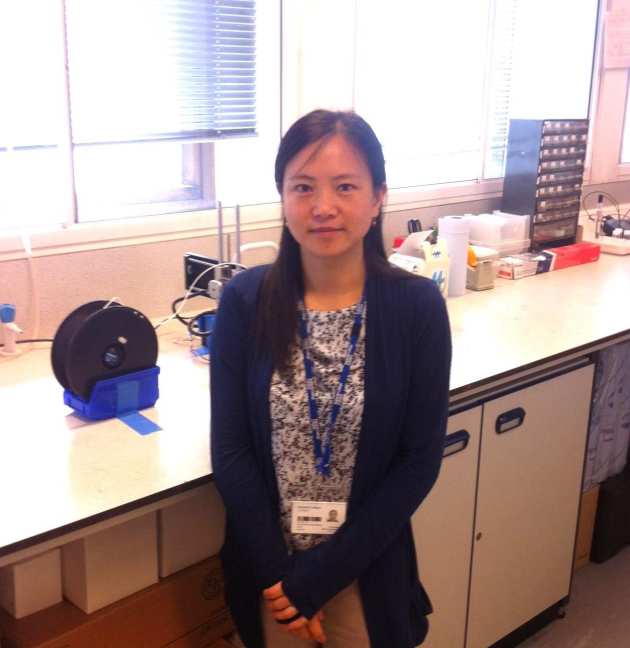
Dr. Jiahui Qi is a materials scientist, microscopist, and chemical engineer. Jiahui was trained as an engineer and chemist and has obtained a Masters Degree (Sichuan University 2002) and PhD (Sheffield University 2011) in Chemical Engineering. With over 10 years of experience in academia and industry, Jiahui has developed expertise in various areas, including crystallisation, materials characterisation, corrosion, and tribology. Her research focuses on utilising advanced electron microscopy and other cutting-edge techniques for characterising material degradation processes due to mechanical impacts, chemical reactions, and corrosion in both toxic and conventional environments.

If you have questions about your application or research area, please do get in touch with our Technical Director, Dr. Shayz Ikram, by email below, or call (01372) 378822.
New Publication Alert from NanoMEGAS!
While studying the structure of beam-sensitive “as-made” ITQ-52 zeolite, NanoMEGAS has demonstrated that it is possible to achieve a similar electron dose using stepwise precession data compared to continuous rotation data, with the right beam blanking techniques. Congratulations to all the authors for this outstanding work! See more here >>